Many companies care about the quality of their service, product, or reputation. This post will highlight why quality is important in the workplace. Plus, it includes 50 interview questions about quality.
Get more interview questions.
Sign up for Huntr to access interview questions tailored to the job you're applying for.
What is quality?
Quality, in the context of soft skills, refers to the degree of excellence or superiority that an individual brings to their work and interactions. It encompasses a commitment to delivering results that meet or exceed expectations, attention to detail, and a continuous pursuit of improvement. Quality as a soft skill is about taking pride in one’s work, being reliable, and consistently striving to enhance one’s abilities and outputs. It involves a proactive attitude towards problem-solving, an openness to feedback, and the flexibility to adapt to new challenges. Ultimately, quality is about adding value in every task undertaken and contributing positively to the overall objectives of a team or organization.
Why is quality important in the workplace?
1. Ensures High Standards
Quality as a skill is paramount in the workplace because it guarantees that all tasks and projects are completed to the highest standards. This not only reflects well on the company's reputation but also ensures customer satisfaction, leading to repeat business and positive word-of-mouth referrals. Employees who prioritize quality in their work contribute to a culture of excellence, setting a benchmark for others to follow.
2. Reduces Costs and Increases Efficiency
Emphasizing quality in the workplace means that tasks are done correctly the first time, significantly reducing the need for rework, which can be costly and time-consuming. This skill in maintaining quality standards helps in streamlining processes and improving efficiency, allowing the company to allocate resources more effectively and focus on innovation and growth.
3. Enhances Team Morale and Job Satisfaction
When quality is a key focus in the workplace, it fosters a sense of pride among employees in their work. Knowing that they are contributing to something of high standard and value can greatly improve job satisfaction and team morale. This, in turn, can lead to higher levels of engagement, lower turnover rates, and a more motivated workforce committed to the company’s success.
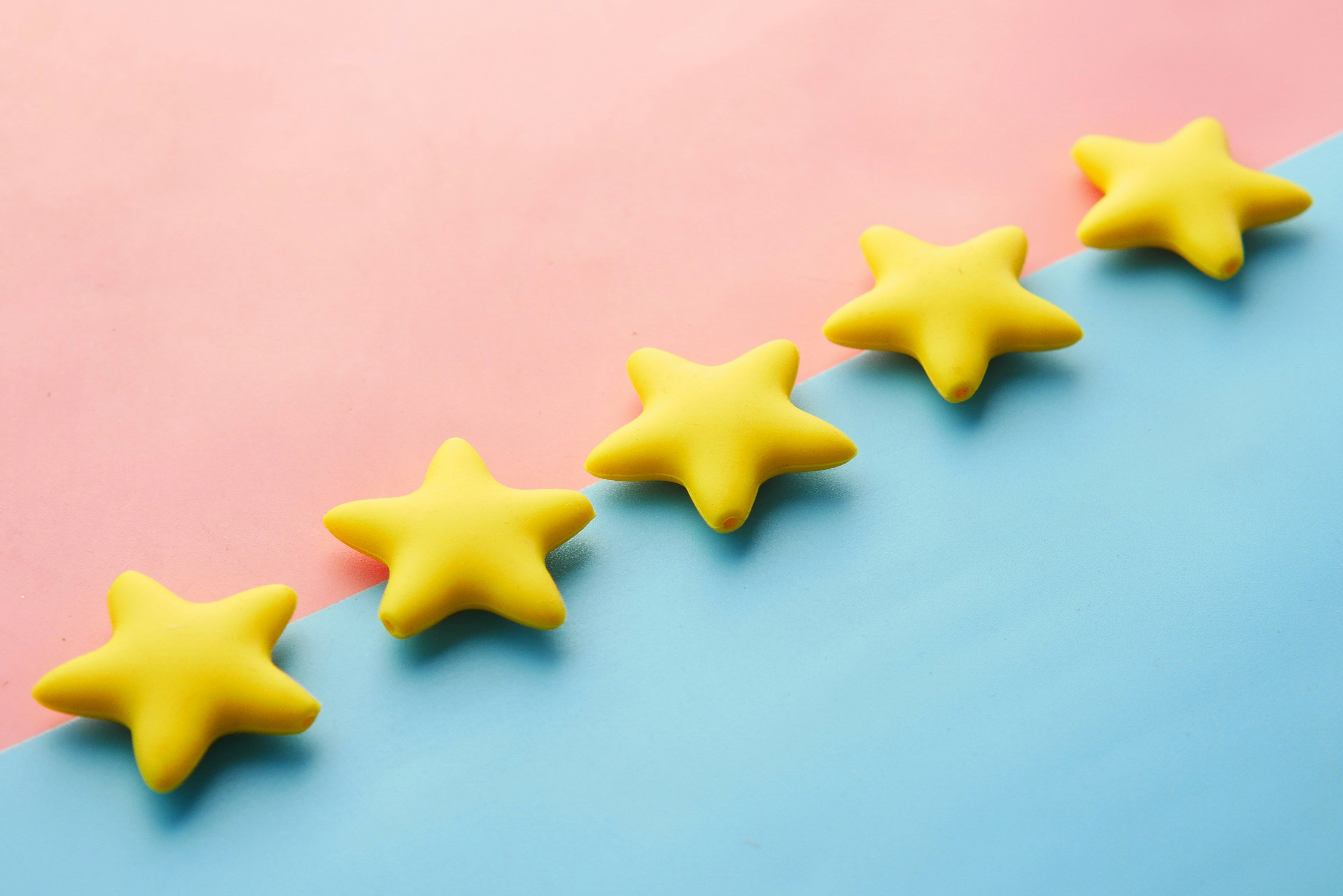
5 Tips for a Quality-Based Interview
Quality is a crucial aspect of any job, reflecting on both the individual's work and the company's reputation. When preparing for an interview that will likely probe into your quality-related skills, it's important to articulate how you can contribute to maintaining or enhancing the standards of your potential employer's products or services. Here are five tips to effectively answer quality-related interview questions:
1. Highlight Your Attention to Detail
Quality is all about the finer points. When discussing your experience, emphasize instances where your keen eye for detail led to significant improvements in a project or process. Use specific examples to demonstrate how your ability to notice and address minor issues prevented larger problems and contributed to the overall quality.
2. Showcase Your Problem-Solving Skills
Employers value candidates who can identify issues and think critically to solve them efficiently. Share examples of how you've identified quality-related problems in the past and the steps you took to resolve them. This will show your proactive approach and commitment to maintaining high standards.
3. Discuss Your Knowledge of Quality Standards
Depending on your industry, there might be specific quality standards or frameworks that companies adhere to, such as ISO 9001. Mention any relevant certifications you have or experiences where you ensured compliance with these standards, demonstrating your understanding of the importance of regulatory and quality guidelines.
4. Talk About Continuous Improvement
Quality is not a one-time achievement but a continuous process. Discuss how you have contributed to continuous improvement initiatives or how you regularly seek feedback to enhance the quality of your work. This shows your commitment to development and your proactive stance on quality management.
5. Explain How You Balance Quality with Efficiency
While quality is paramount, efficiency cannot be overlooked. Employers look for candidates who can deliver high-quality work within reasonable timeframes. Provide examples of how you've managed to maintain or enhance quality without compromising on efficiency, demonstrating your ability to prioritize and manage your time effectively.
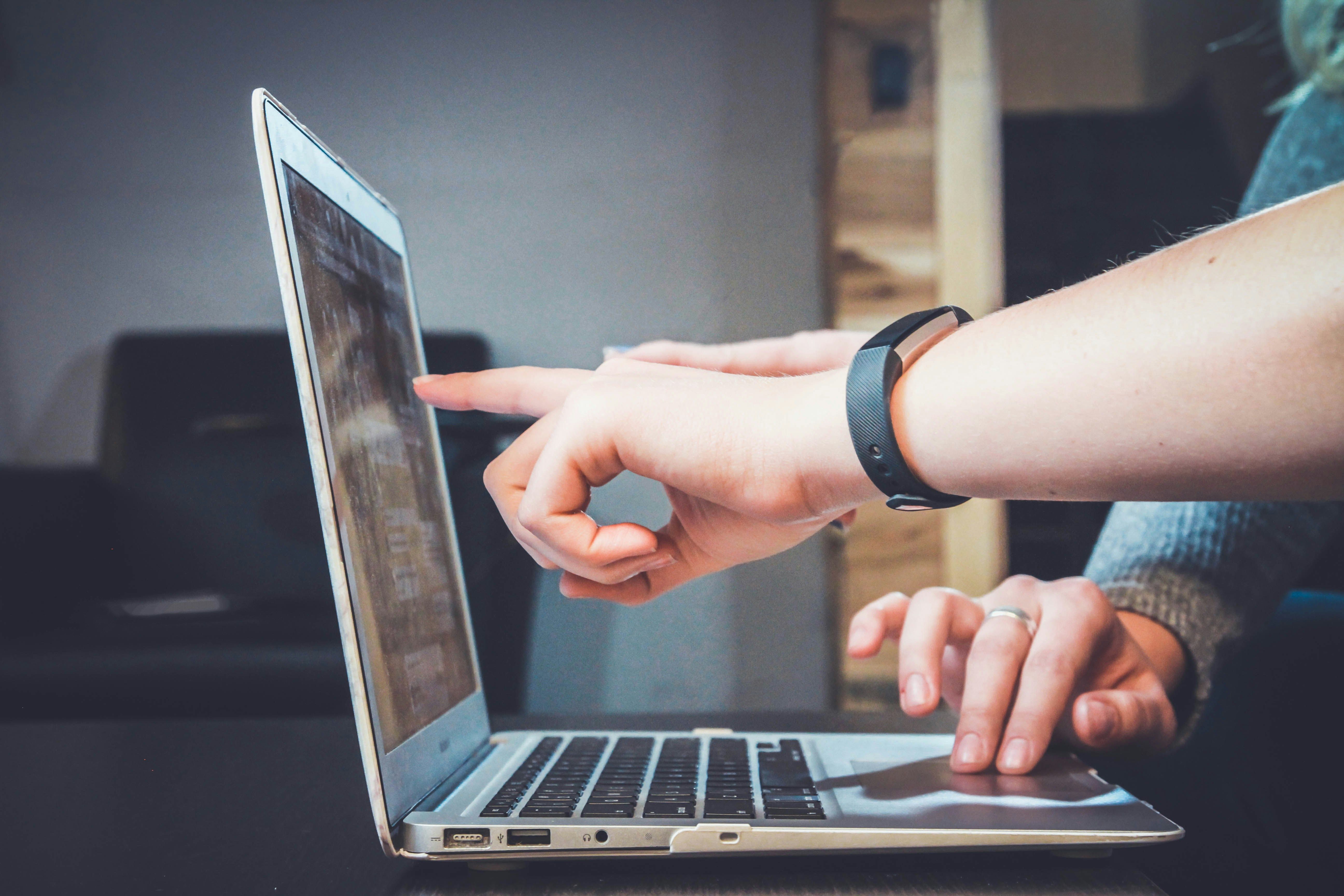
50 Interview Questions About Quality (With Answers)
1. How do you define "quality" in your industry?
Quality in our industry is defined by meeting or exceeding customer expectations and delivering products or services that are reliable, consistent, and free from defects. It encompasses factors like performance, durability, safety, and customer satisfaction.
2. What measures do you take to ensure the highest quality of your products/services?
We implement a comprehensive quality management system that includes rigorous testing, regular inspections, and adherence to industry standards and regulations. Continuous training for our team members, robust documentation of processes, and proactive risk management also contribute to ensuring high quality.
3. Can you describe a situation where you had to improve the quality of a product/service? How did you go about it?
In a previous role, we received customer feedback indicating issues with product durability. We conducted a root cause analysis, collaborated with engineering and production teams to identify improvements, implemented stricter quality control measures in manufacturing, and conducted thorough testing before product release. This approach resulted in a significant improvement in product quality and customer satisfaction.
4. What role does customer feedback play in your quality assurance process?
Customer feedback is invaluable in identifying areas for improvement and understanding customer expectations. We use feedback mechanisms such as surveys, reviews, and direct communication channels to gather insights, which then inform our quality assurance strategies and continuous improvement efforts.
5. How do you balance the need for high quality with cost constraints?
We prioritize cost-effective solutions without compromising on quality by optimizing processes, leveraging technology for efficiency gains, and collaborating closely with suppliers to negotiate favorable terms without sacrificing quality standards. We also conduct cost-benefit analyses to make informed decisions.
6. What quality control tools or methods do you find most effective?
I find tools like Six Sigma, Statistical Process Control (SPC), and Failure Mode and Effects Analysis (FMEA) highly effective in identifying and addressing quality issues. These tools help in systematic problem-solving, process optimization, and risk mitigation, leading to improved quality outcomes.
7. How do you ensure the quality of materials or components you source from external suppliers?
We have stringent supplier evaluation and qualification processes in place, including audits, quality certifications, and performance monitoring. We establish clear quality requirements in contracts, conduct incoming inspections, and collaborate closely with suppliers to address any quality issues promptly.
8. In what ways do you think technology has impacted the quality of products/services in your industry?
Technology has significantly improved quality in our industry through automation, data analytics, real-time monitoring, and predictive maintenance. It enables faster and more accurate quality assessments, proactive identification of issues, and continuous optimization of processes, ultimately leading to higher-quality products and services.
9. How do you measure the success of your quality improvement initiatives?
We measure success through key performance indicators (KPIs) such as defect rates, customer satisfaction scores, product reliability metrics, and compliance with quality standards. Regular audits, internal reviews, and benchmarking against industry best practices also help in evaluating the effectiveness of our quality improvement initiatives.
10. Can you discuss a time when you had to make a trade-off between quality and another factor? How did you make your decision?
n a previous project, we faced a tight deadline to launch a new product while maintaining high quality. We had to make trade-offs in terms of certain features and functionalities to meet the deadline. To make this decision, we conducted a thorough risk assessment and prioritized the core features essential for product functionality and customer satisfaction. We communicated transparently with stakeholders about the trade-offs and focused on delivering the best possible quality within the given constraints.
11. What role do employees at all levels play in maintaining the quality standards of your company?
Employees at all levels play a crucial role in maintaining quality standards by following established processes, adhering to quality guidelines, participating in continuous training and improvement initiatives, and actively contributing feedback and suggestions for quality enhancements. Their commitment to quality and attention to detail directly impact the overall quality culture of the company.
12. How do you keep up with the evolving standards of quality in your industry?
We stay updated with evolving quality standards through continuous industry research, participation in professional development programs and conferences, networking with industry experts, and maintaining strong relationships with regulatory bodies and standards organizations. We also conduct regular internal reviews and audits to ensure alignment with the latest quality requirements and best practices.
13. What are the biggest challenges you face in maintaining high-quality standards?
One of the biggest challenges is balancing innovation and agility with maintaining consistent quality. Rapid changes in technology, market demands, and regulatory landscapes require us to adapt quickly without compromising on quality. Managing supplier quality and ensuring seamless integration across different departments or teams also present ongoing challenges.
14. How do you ensure that new hires understand and commit to your quality standards?
We have a comprehensive onboarding process that includes thorough training on quality standards, procedures, and expectations. We emphasize the importance of quality in achieving company goals and customer satisfaction during orientation sessions. Regular feedback, coaching, and performance evaluations also reinforce adherence to quality standards among new hires.
15. How has the concept of quality changed in your industry over the past decade?
Over the past decade, the concept of quality in our industry has evolved to include not just product performance and reliability but also factors like sustainability, user experience, data security, and regulatory compliance. There's a greater emphasis on customer-centric quality metrics, continuous improvement through data-driven insights, and proactive risk management strategies.
16. Can you give an example of a project that did not meet quality expectations and how you handled it?
In a recent project, we encountered unexpected quality issues during the testing phase that affected product performance. We immediately halted production, conducted a thorough root cause analysis, involved cross-functional teams to identify solutions, implemented corrective actions, and retested extensively to ensure quality standards were met before relaunching the product. Transparent communication with stakeholders throughout the process helped rebuild trust and reinforce our commitment to quality.
17. How do you incorporate sustainability into your quality assurance processes?
We integrate sustainability considerations into our quality assurance processes by evaluating environmental impacts throughout the product lifecycle, implementing eco-friendly practices in manufacturing and sourcing, complying with relevant sustainability standards and certifications, and fostering a culture of environmental responsibility among employees. Sustainability metrics are included in our quality KPIs to ensure alignment with our sustainability goals.
18. How do you manage quality control across different locations or departments?
We establish standardized quality control protocols, processes, and performance metrics that apply uniformly across all locations and departments. Regular training, audits, and quality reviews ensure consistent adherence to quality standards. We also leverage technology solutions for real-time monitoring, data analytics, and collaboration to streamline quality control efforts across diverse locations or departments.
19. What certifications or awards has your company received related to quality?
Our company has been awarded the ISO 9001 certification for our quality management system, which reflects our commitment to meeting international quality standards. We have also received industry-specific quality awards recognizing our excellence in product quality, customer satisfaction, and continuous improvement efforts.
20. How do you prioritize areas for quality improvement?
We prioritize areas for quality improvement by conducting comprehensive assessments of customer feedback, performance metrics, risk analyses, and industry benchmarks. We also involve key stakeholders in prioritization discussions to align improvement efforts with strategic goals and address critical issues that have the most significant impact on quality and customer satisfaction.
21. In what ways do you believe that investing in quality impacts customer satisfaction and loyalty?
Investing in quality directly impacts customer satisfaction and loyalty by ensuring consistent product/service performance, reliability, and meeting or exceeding customer expectations. High-quality products/services result in fewer defects, improved user experience, increased trust in the brand, and higher customer retention rates. Positive word-of-mouth referrals and customer advocacy also contribute to long-term customer loyalty.
22. How do you train your team on quality control processes and tools?
We provide comprehensive training programs on quality control processes, tools, and best practices to our team members. Training includes hands-on workshops, online modules, certification courses, and continuous learning opportunities. We also encourage knowledge sharing, cross-functional collaboration, and regular skills assessments to ensure our team remains proficient in quality control methodologies.
23. Can you explain the difference between quality assurance and quality control in your work?
Quality assurance focuses on preventing defects and ensuring that processes are in place to deliver consistent quality throughout the product/service lifecycle. It involves establishing standards, guidelines, and procedures, conducting audits, and implementing preventive measures to improve processes.
On the other hand, quality control involves inspecting, testing, and verifying products/services to identify defects and deviations from quality standards. It includes activities such as product testing, data analysis, corrective actions, and continuous monitoring to maintain quality levels.
24. How do you ensure that your quality standards are aligned with customer expectations?
We ensure alignment with customer expectations by actively seeking and analyzing customer feedback, conducting market research, engaging with customers through surveys and focus groups, and monitoring customer satisfaction metrics. We incorporate customer preferences, needs, and feedback into our quality standards, product/service design, and improvement initiatives to deliver value and meet or exceed customer expectations.
25. What is your approach to handling customer complaints related to quality?
Our approach to handling customer complaints related to quality is to prioritize quick resolution, effective communication, and proactive problem-solving. We have dedicated channels for receiving and addressing customer complaints promptly, investigating root causes, implementing corrective actions, and following up with customers to ensure satisfaction. We view customer complaints as opportunities to learn, improve, and demonstrate our commitment to quality and customer service excellence.
26. How do you use data and analytics in your quality management processes?
We use data and analytics extensively in our quality management processes to gather insights, identify trends, track performance metrics, detect anomalies, and make data-driven decisions. We leverage quality management software, statistical tools, dashboards, and reporting mechanisms to analyze quality-related data, monitor key performance indicators, conduct root cause analyses, and continuously improve quality processes and outcomes.=
27. Can you discuss a major quality initiative that you've implemented recently?
One major quality initiative we implemented recently was the adoption of a comprehensive quality management system (QMS) that integrates all quality-related processes, documentation, and workflows into a centralized platform. This initiative streamlined quality assurance, control, and improvement activities, enhanced collaboration among teams, improved data visibility and analysis capabilities, and strengthened our overall quality management practices.
28. How do you ensure continuous improvement in the quality of your products/services?
We ensure continuous improvement in quality by fostering a culture of innovation, learning, and continuous improvement across the organization. This includes regular reviews of quality performance, conducting root cause analyses, implementing corrective and preventive actions, soliciting feedback from stakeholders, benchmarking against industry standards, investing in R&D and technology upgrades, and empowering employees to contribute ideas for quality enhancements.
29. What role does leadership play in fostering a culture of quality?
Leadership plays a crucial role in fostering a culture of quality by setting clear expectations, priorities, and standards for quality throughout the organization. Effective leaders communicate the importance of quality, provide resources and support for quality initiatives, lead by example, empower employees to take ownership of quality, promote collaboration and continuous improvement, and recognize and reward achievements related to quality. They also establish accountability, promote transparency, and create a culture of learning and innovation that encourages feedback and adaptation based on quality insights.
30. How do you assess the risk of quality issues in new projects or products?
We assess the risk of quality issues in new projects or products through comprehensive risk assessments that consider factors such as complexity, novelty, scope, resources, timelines, supplier/vendor capabilities, regulatory requirements, and potential impact on customers and stakeholders. We use risk management tools, techniques, and methodologies to identify, prioritize, analyze, and mitigate risks related to quality, and we involve cross-functional teams in risk assessment and decision-making processes to ensure thorough evaluations and proactive risk management strategies.
31. What are the most common misconceptions about quality in your industry?
One common misconception about quality in our industry is that it's solely the responsibility of the quality control or assurance department. In reality, quality is a collective responsibility that involves every individual, department, and process within the organization. Another misconception is equating quality with perfection, whereas quality is about meeting customer requirements, continuous improvement, and delivering value. Additionally, some may view quality as a cost center rather than a strategic investment that enhances competitiveness, customer satisfaction, and long-term success.
32. How do you ensure quality in a fast-paced production environment?
In a fast-paced production environment, we ensure quality by implementing robust quality management systems, standardized processes, clear quality control checkpoints, real-time monitoring and feedback mechanisms, automated quality assurance tools, regular training and skills development for employees, and continuous performance evaluations. We also prioritize preventive measures, rapid problem-solving, agile adaptations, and collaboration across teams to address quality issues promptly and maintain quality standards amidst rapid production cycles and changing demands.
33. Can you describe a time when maintaining quality helped you gain a competitive advantage?
Certainly. In a previous project, our focus on maintaining high-quality standards throughout the product development and production process allowed us to differentiate ourselves in the market. Customers appreciated the reliability, durability, and performance of our products, leading to positive reviews, repeat business, and referrals. This reputation for quality helped us gain a competitive advantage by attracting new customers, retaining existing ones, and enhancing our brand image as a trusted provider of high-quality solutions.
34. How do you manage the quality of outsourced or subcontracted work?
We manage the quality of outsourced or subcontracted work through rigorous vendor selection processes, clear contractual agreements with quality clauses, regular performance evaluations, quality audits and inspections, ongoing communication and collaboration with suppliers/subcontractors, adherence to quality standards and specifications, and timely resolution of quality issues. We also provide training, guidance, and support to external partners to ensure alignment with our quality expectations and objectives.
35. What impact has social media had on your quality control processes?
Social media has had a significant impact on our quality control processes by providing valuable insights, feedback, and sentiment analysis from customers, stakeholders, and the public. We monitor social media platforms for discussions, reviews, complaints, and trends related to our products/services, brand reputation, and customer experiences. This real-time feedback helps us identify quality issues, address customer concerns, improve product/service offerings, enhance communication strategies, and proactively manage our reputation and customer relationships.
36. How do you anticipate and address potential quality issues in product design?
We anticipate and address potential quality issues in product design through thorough design reviews, risk assessments, prototyping, simulations, usability testing, failure mode and effects analysis (FMEA), and cross-functional collaboration among design, engineering, manufacturing, and quality assurance teams. We also engage customers, gather requirements, conduct market research, benchmark against industry standards, and consider lessons learned from past projects to inform our design decisions, mitigate risks, and ensure that quality is built into the product from the initial stages of development.
37. What are the key indicators you look for that suggest a quality improvement is needed?
Key indicators that suggest a quality improvement is needed include customer complaints or feedback trends, increasing defect rates or failure rates, deviations from quality standards or specifications, recurring quality issues, declining customer satisfaction scores, competitive benchmarking results, regulatory non-compliance issues, internal audit findings, and opportunities for process optimization or efficiency gains. We also monitor key performance indicators (KPIs) related to quality, such as first-pass yield, rework rates, scrap rates, and cycle times, to identify areas for improvement and measure the effectiveness of quality improvement initiatives.
38. How do you involve customers in your quality assessment process?
We involve customers in our quality assessment process through various channels such as surveys, feedback forms, focus groups, interviews, user testing, and online reviews. We actively seek and analyze customer input regarding their experiences, preferences, satisfaction levels, and suggestions for improvement. Customer feedback is a valuable source of qualitative and quantitative data that informs our quality assessment, helps us identify areas for enhancement, and ensures that our products/services align with customer needs and expectations.
39. What challenges do you face in maintaining quality during rapid growth or scaling?
Maintaining quality during rapid growth or scaling presents several challenges, including maintaining consistency across increased production volumes, managing supply chain complexities, ensuring workforce competency and capacity, adapting processes to higher demand levels, and maintaining customer satisfaction amidst expansion. Other challenges include balancing speed with quality, optimizing resources and infrastructure, implementing robust quality control systems, and proactively addressing potential risks and bottlenecks associated with growth. Effective planning, resource allocation, continuous monitoring, agility, and stakeholder collaboration are essential in overcoming these challenges and sustaining quality during periods of rapid growth.
40. How do you ensure the durability and longevity of your products as part of your quality standards?
We ensure the durability and longevity of our products as part of our quality standards through rigorous testing, quality assurance processes, adherence to industry standards and regulations, use of high-quality materials and components, continuous product improvement efforts, and customer feedback integration. We conduct reliability testing, stress testing, environmental testing, and lifecycle assessments to validate product durability and performance under various conditions. Additionally, we monitor product performance in the field, collect reliability data, and use predictive analytics to anticipate and address potential issues that may affect product longevity.
41. Can you discuss the role of automation in quality control?
Automation plays a significant role in quality control by streamlining processes, reducing human error, improving efficiency, enhancing accuracy, increasing scalability, and enabling real-time monitoring and data analysis. Automated quality control systems encompass various technologies such as sensors, robotics, artificial intelligence, machine learning, data analytics, and digital platforms. These systems automate inspection, testing, measurement, calibration, documentation, and reporting tasks, allowing for consistent and standardized quality assessments across production cycles. Automation also facilitates predictive maintenance, anomaly detection, continuous improvement, and compliance with quality standards and regulations.
42. How do you balance innovation with maintaining consistent quality?
We balance innovation with maintaining consistent quality by integrating quality considerations into the innovation process, fostering a culture of quality and innovation, establishing clear quality criteria and metrics for new initiatives, conducting thorough risk assessments, leveraging technology and data-driven insights, involving cross-functional teams in decision-making, and prioritizing customer value and feedback. We embrace agile methodologies, iterative testing, prototyping, and validation to ensure that innovative solutions meet quality standards, address customer needs, and deliver measurable benefits. Continuous learning, adaptation, and collaboration are key in striking a balance between innovation and quality.
43. What impact do you think AI and machine learning will have on quality management?
AI and machine learning are revolutionizing quality management by enabling predictive analytics, automated decision-making, real-time monitoring, anomaly detection, root cause analysis, pattern recognition, and continuous improvement. These technologies enhance quality control processes by identifying trends, optimizing workflows, reducing defects, enhancing efficiency, and proactively addressing quality issues before they escalate. AI-driven quality management systems also facilitate data-driven insights, risk management, resource optimization, and regulatory compliance, leading to higher levels of quality, productivity, and competitiveness in the industry.
44. How do you ensure ethical practices are maintained as part of your quality standards?
We ensure ethical practices are maintained as part of our quality standards through clear policies, codes of conduct, ethical guidelines, compliance frameworks, training programs, and ongoing monitoring and enforcement mechanisms. Our ethical standards encompass integrity, transparency, fairness, respect for human rights, environmental responsibility, safety, and compliance with laws and regulations. We promote ethical decision-making, ethical leadership, and a culture of integrity and accountability throughout the organization. Regular audits, ethical reviews, whistleblower mechanisms, and stakeholder engagement also play a role in upholding ethical practices and maintaining trust with customers, partners, and the community.
45. What steps do you take to recover from a major quality failure?
In the event of a major quality failure, we take immediate action to mitigate the impact, address root causes, communicate transparently with stakeholders, and implement corrective and preventive measures to prevent recurrence. Our steps typically include conducting a thorough investigation, identifying contributing factors, assessing the extent of the impact, notifying affected parties, implementing containment actions, developing an action plan, allocating resources, assigning responsibilities, monitoring progress, and providing regular updates. We also prioritize customer satisfaction, reputation management, and continuous improvement throughout the recovery process.
46. How do you deal with varying quality standards in different markets or regions?
We deal with varying quality standards in different markets or regions by conducting comprehensive market research, understanding local regulations, cultural preferences, customer expectations, and competitive landscapes, and adapting our quality management strategies accordingly. We establish global quality standards while allowing for flexibility and customization to meet regional requirements and market demands. Collaboration with local partners, suppliers, and regulatory bodies, cross-functional coordination, consistent communication, and knowledge sharing are key in ensuring alignment with diverse quality standards and maintaining a high level of quality across markets.
47. How do you ensure compliance with international quality standards?
Ensuring compliance with international quality standards involves several key practices. First, we conduct thorough research to understand the specific standards and regulations applicable to our industry and target markets. We then integrate these standards into our quality management system, policies, and procedures. Regular audits, inspections, and assessments are conducted to verify compliance and identify areas for improvement. Training programs and workshops are also provided to educate employees on international quality standards and best practices. Collaboration with industry experts, certification bodies, and regulatory agencies further supports our efforts to maintain compliance and uphold high-quality standards across borders.
48. What role does cross-functional collaboration play in quality management?
Cross-functional collaboration plays a crucial role in quality management as it brings together diverse perspectives, expertise, and resources to achieve common quality goals. Collaboration between departments such as production, engineering, design, quality assurance, supply chain, and customer service fosters communication, coordination, and synergy in addressing quality issues, implementing improvements, and driving continuous quality enhancement initiatives. By working collaboratively, teams can identify root causes of quality problems, implement preventive measures, streamline processes, share best practices, leverage technology, and align efforts to meet customer expectations and business objectives effectively.
49. How do you see the future of quality management evolving?
The future of quality management is poised for significant advancements driven by technological innovations, digitalization, data analytics, automation, artificial intelligence, and predictive modeling. These developments will enable real-time monitoring, proactive risk management, predictive maintenance, agile decision-making, and personalized quality solutions tailored to individual customer needs. Quality management will become more integrated with overall business strategies, focusing on value creation, customer experience, sustainability, and continuous improvement. Collaboration, transparency, agility, and adaptability will be key pillars of future quality management practices, enabling organizations to stay competitive, resilient, and responsive to changing market dynamics and customer expectations.
50. Can you share a success story where a focus on quality made a significant impact on your business?
Certainly! One notable success story where a focus on quality made a significant impact on our business was during the launch of a new product line. Our team conducted extensive market research, customer surveys, and prototype testing to ensure that the product met stringent quality standards and addressed key customer pain points. We implemented robust quality control measures throughout the production process, including thorough inspections, testing protocols, and supplier quality management. As a result of our focus on quality, the new product line received overwhelmingly positive feedback from customers, leading to increased sales, market share growth, and enhanced brand reputation. Our commitment to quality not only drove customer satisfaction and loyalty but also contributed to operational efficiency, reduced defects, and improved overall business performance. This success story reinforced the importance of quality as a strategic differentiator and a driver of business success in a competitive marketplace.